Errors and Tips
Areas of Improvement
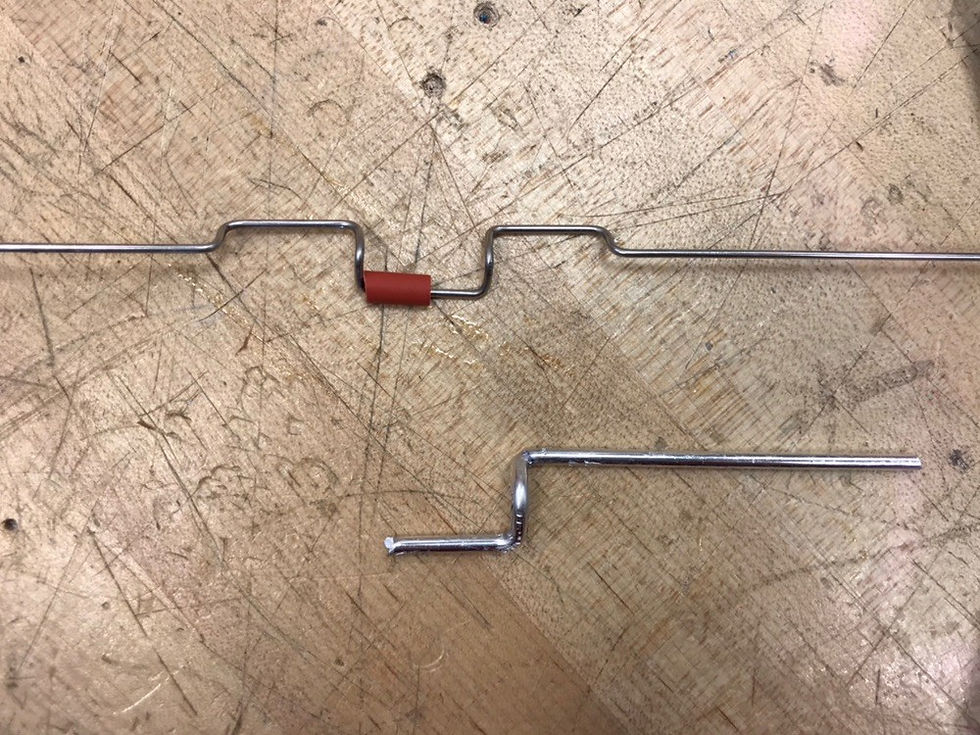

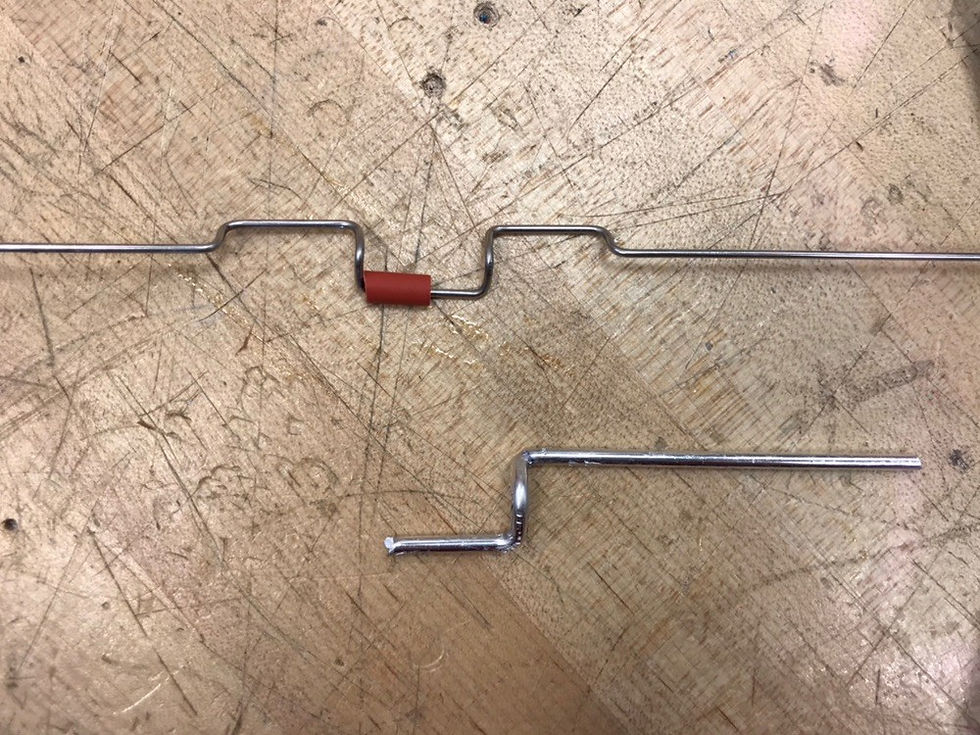
Crankshaft
Copper is too soft to withstand the motion of the power and displacement pistons.
Bending the shaft by hand is imprecise and increases the risk of material failure.
The dimensions of the crankshaft were also very sensitive to the power piston, so we speculate that this could be a major reason behind the failure of our engine.
We suggest seeking professional advice from the Machine Shop!
Piston-shaft supports
We tried to use ice-cream sticks to translate the motion of the power piston to the crankshaft, but they snapped when we attempted to drill holes through them.
We suggest laser cutting these supports out of scrap acrylic at the Innovation Studio.
Even so, we could have improved the rigidity of the acrylic sticks by implementing a cross bar between them. Rigidity is important as it restricts motion to the vertical axis and minimize others that impact the balance of the crankshaft.
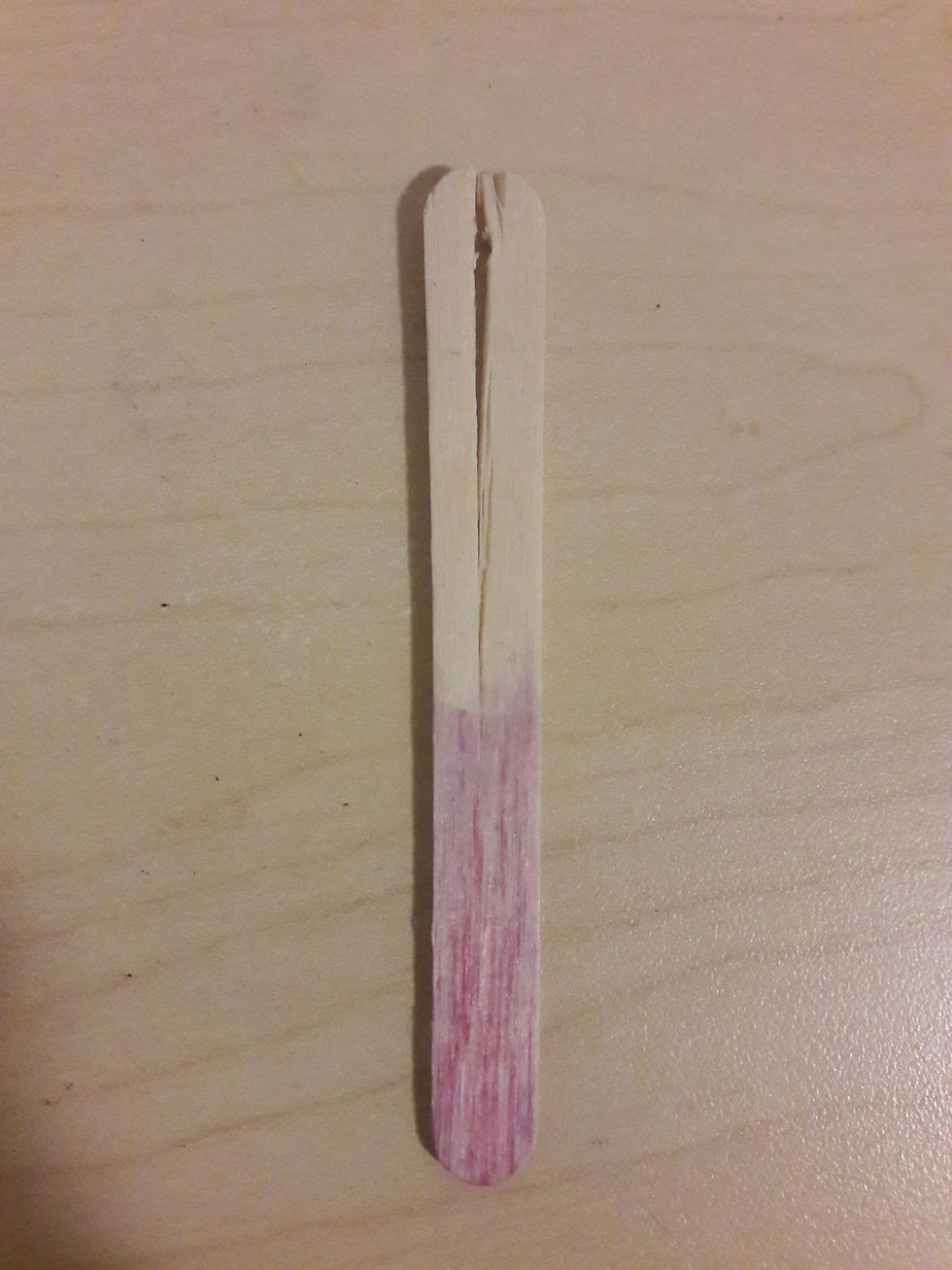

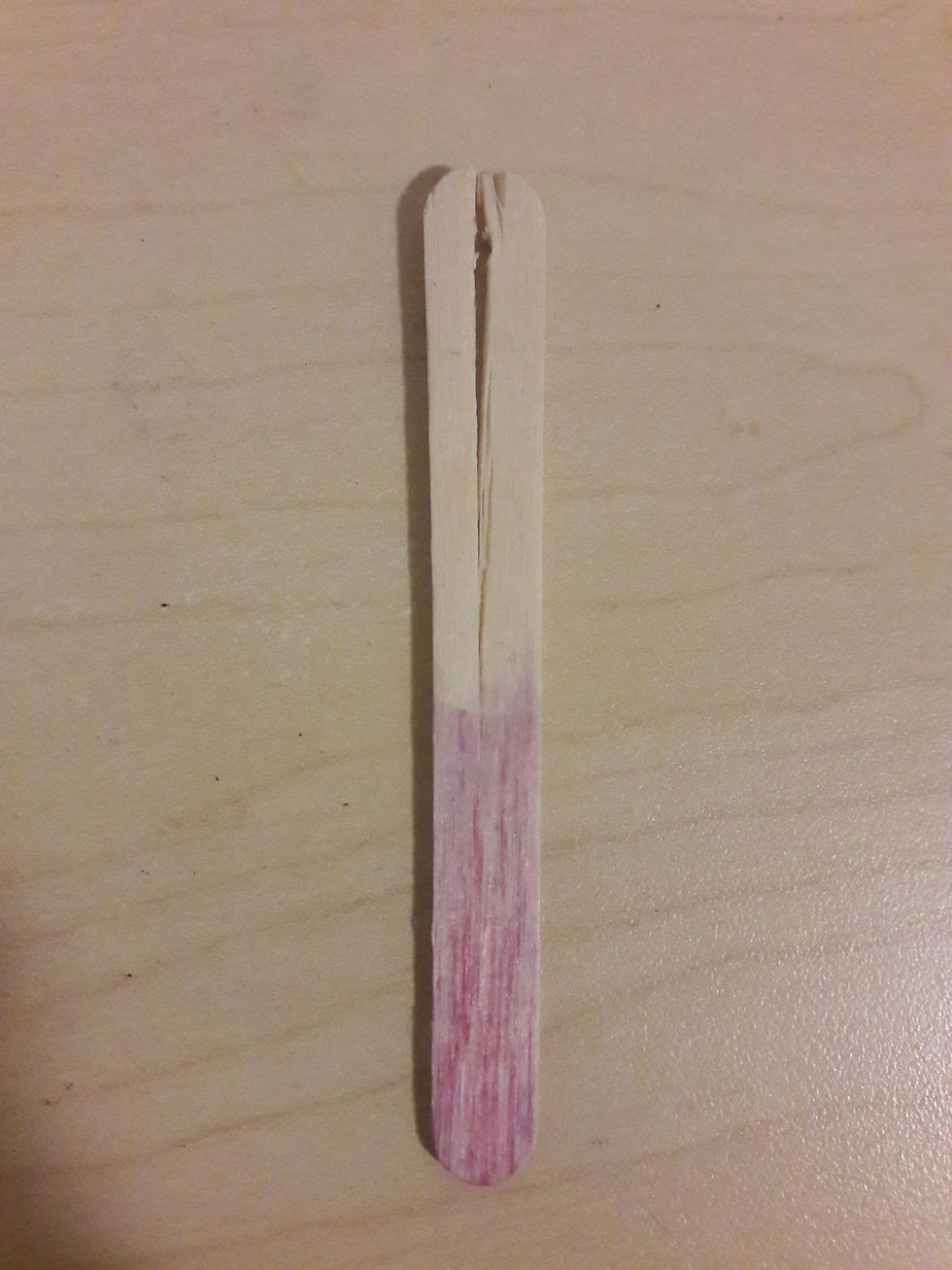



Engine Body
We used an air freshener can for our engine body, but on hindsight, we could have used a metal can with a larger diameter. A larger diameter gives us a larger volume of air to manipulate which also leads to the engine having a higher potential power output.
Our current can has a concave bottom so we were unable to get the flame as close to the bottom as we would like without stifling it.
With more time, we could have used a larger, flat bottom can. Getting the flame closer to the bottom of the can is essential as it directly affects the heat transferred into the air at the bottom of the can. The higher the temperature of the air at the bottom of the can, the higher the pressure at the bottom of the can. This increases the probability of our engine succeeding to work.
Power Piston
We used a balloon backed with circular cardboard pieces as our power piston.
However, there is significant resistance when the crankshaft tries to raise the balloon. This creates friction that we are unable to get rid of without changing the power piston design.
If we had more time/resources, we would attempt to experiment with a few other power piston designs. For example: of some ideas include using a smaller cardboard piece, different sized balloons, etc.

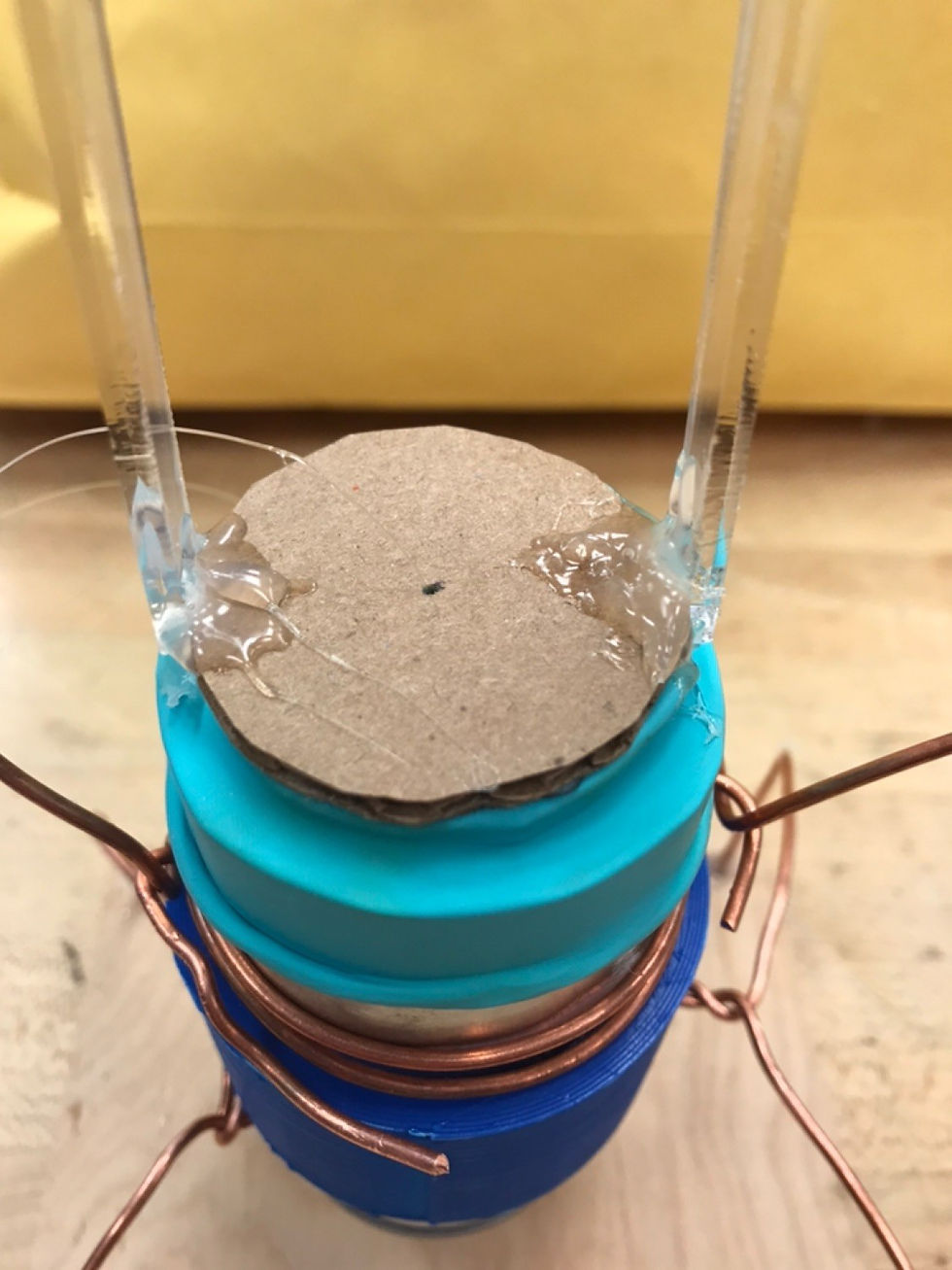


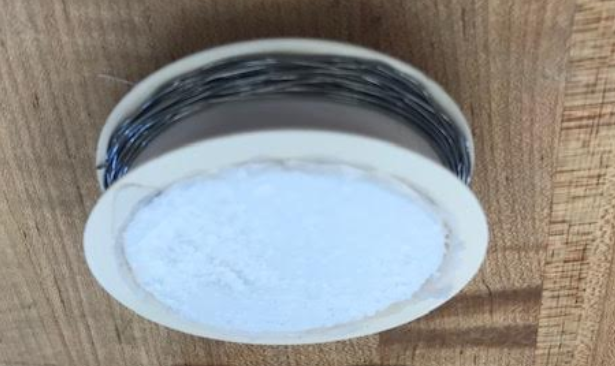

Flywheel
A flywheel with a high moment of inertia is important so that it is able to maintain its rotational speed. Our flywheel consisted of a tape reel weighted around the outside with soldering wire.
Feedback from Professor Liebenberg informed us that our flywheel was too small.
With more time, we could probably experiment with a number of different sized flywheels to determine the suitable one for our engine.
Tips
There is always space for improvement even had our Stirling engine worked. Every time we test in a certain configuration, we can always find areas where we can implement incremental improvements.
For example, adjusting how taut the balloon was pulled across the cylinder, how high the crankshaft was raised and how much wire was wrapped around the flywheel.
If we had more time, we would have fine-tuned the dimensions of the crankshaft by carrying out more experiments.


